Salesforce for Manufacturing: Boost Efficiency with Document Generation, OCR & File Storage
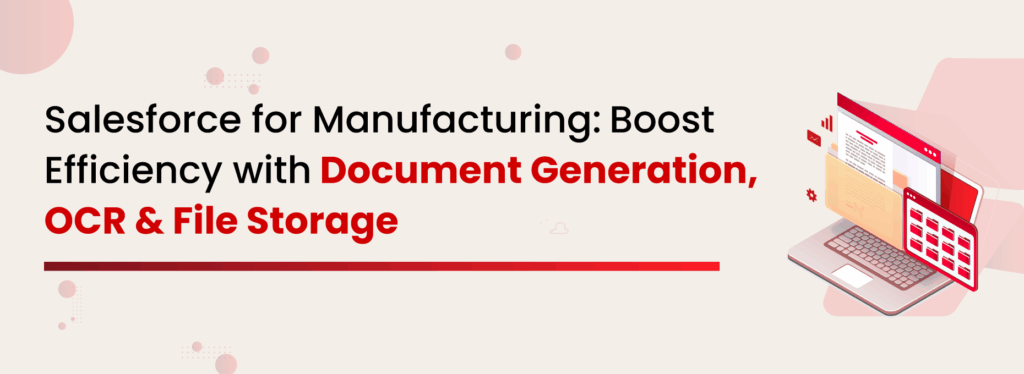
In the manufacturing industry, managing documents goes beyond merely keeping things organized. It is essential for maintaining compliance, preventing delays, and ensuring that products arrive at the right location at the right time. From purchase orders to quality checks, each step in the process must be executed with precision to ensure this success. But the harsh truth is that most teams are drowning in multiple documents, manual approvals, missed emails, and disorganized file & folders, hindering their efficiency and productivity. So, how can manufacturing companies break free from document overload and build a system that truly works? The Answer: Leveraging Salesforce with Smart Document Management Solutions Why? Because Salesforce is transforming the way manufacturers operate. With Salesforce Manufacturing Cloud, you can do more than manage customer relationships. By connecting sales, operations, and partners on a single platform, you gain better visibility, smarter forecasts, and control over every step. But even with all that power, there’s one thing that still clogs the gears: the document-heavy manufacturing process itself. Think about it, Purchase Order Management, Production & Quality Control, and Inventory Management, they’re all document-heavy, approval-driven, and deadline-sensitive. If you’re still stuck in manual mode, it doesn’t matter how powerful your CRM is, you’re always prone to errors, delays, and inefficiencies. That’s where document automation and external document management systems come in. When these integrate seamlessly with Salesforce, everything clicks into place. That’s when you stop wasting time on manual file management and start speeding up processes across the board. In this blog, we’ll break down exactly how all of this fits into your manufacturing process—from purchase orders to quality control—and why automating documents is the next step in building a more efficient, scalable operation. Purchase Order Management Picture this. Your purchase team urgently needs to source materials for an upcoming manufacturing unit. They’ve found a few solid vendors, and it’s time to request quotes, negotiate pricing, and raise a purchase order. Sounds straightforward? Not really. Here’s how it usually plays out: You raise a purchase request, which goes to the Department Head for approval and then to the Procurement Head. Once it’s green-lit, the RFQs go out, vendor quotes trickle in, and after some evaluation, you generate the Purchase Order(PO). The vendor confirms, shares invoices, and sets delivery timelines. But now you’re juggling Work Orders, Bill of Materials(BOMs), Vendor Quotations, Inspection Reports, NCRs, and of course, contracts. Production & Quality Control Once the PO is confirmed and the materials start arriving, it’s time to get into the thick of production. This is where your operations team kicks into high gear, and where the paperwork continues to pile up. From production schedules to inspection logs, everything needs to be tracked, verified, and approved Here’s what the usual flow looks like: Materials are received and logged Work Orders are issued Production begins Quality checks kick in at different stages NCRs and inspection reports are generated Final product is approved or sent back for rework You’re now managing Material Inspection Reports, WIP Checklists, QA Forms, NCRs, Compliance Certificates, and final QA sign-offs. Inventory Management With production rolling and quality checks in motion, it’s now up to inventory management to keep everything balanced. Raw materials in, finished goods out, and somewhere in between—real-time stock visibility is everything. Sounds easy in theory, but in practice? Things can get chaotic fast. Here’s how the typical flow goes: Goods are received and logged Inventory levels are updated manually Items are moved to production or storage Finished goods are recorded Dispatch and delivery details are entered Stock reports are generated for finance and procurement teams. You’re now working with GRNs, Stock Transfer Forms, Inventory Count Sheets, Dispatch Notes, and Delivery Challans. But even if you’ve managed to stay on top of these documents so far, it only takes one slip to disrupt the entire chain. Here’s Why Manual Handling of Operational Documents Holds You Back Let me ask you, if a document goes missing, how quickly can your team recover, and at what cost? And when documents are generated manually, how confident are you that every field is filled, every signature captured, and every version tracked? If you don’t know the answer, or if your answer starts with “it depends,” that’s already a cause for concern. Manual processes might’ve worked back when operations were simpler. But today? With everything moving fast and expectations even faster, managing documents by hand is like trying to race a jet with a bicycle. If you manage your Purchase Orders, Vendor Quotes, and Work Orders manually, you already know the pain. One missed email, one outdated version of a BOM (Bill of Materials), or a missed detail in the Inspection Report can suddenly throw your whole workflow off balance. You’ve probably seen it firsthand: That NCR (Non-Conformance Report) form that went missing just before a final quality audit The GRN (Goods Receipt Note) that didn’t make it to the inventory team in time The Dispatch Note that was saved in the wrong folder, delaying shipment The QA Certificate that never got signed off, holding up production There is a risk of missing details when documents are created manually. This issue becomes more pronounced when there is no automated workflow for review and approval. As a result, you may be losing valuable production hours. Many manufacturers assume that implementing multiple software solutions will be expensive and technically overwhelming, but that’s not the case. Did you know document-related issues can cause up to 21.3% productivity loss? A Heavy Equipment Manufacturing Industry, known for powering infrastructure with high-performance machinery like cranes and excavators, struggled with scattered files, poor folder sync, and unclear access controls. That’s when XfilesPro stepped in. By streamlining document storage, syncing, and access management, they increased efficiency, saved time, and ultimately boosted overall productivity. Download the case study to know more Meet XfilesPro: The Automated Document Management Suite You Need XfilesPro is purpose-built for managing documents within Salesforce. It aligns seamlessly with your industry’s compliance and operational needs. Let me walk you through